Zinc Dross Distilling Furnace
Optimal Zinc Recovery
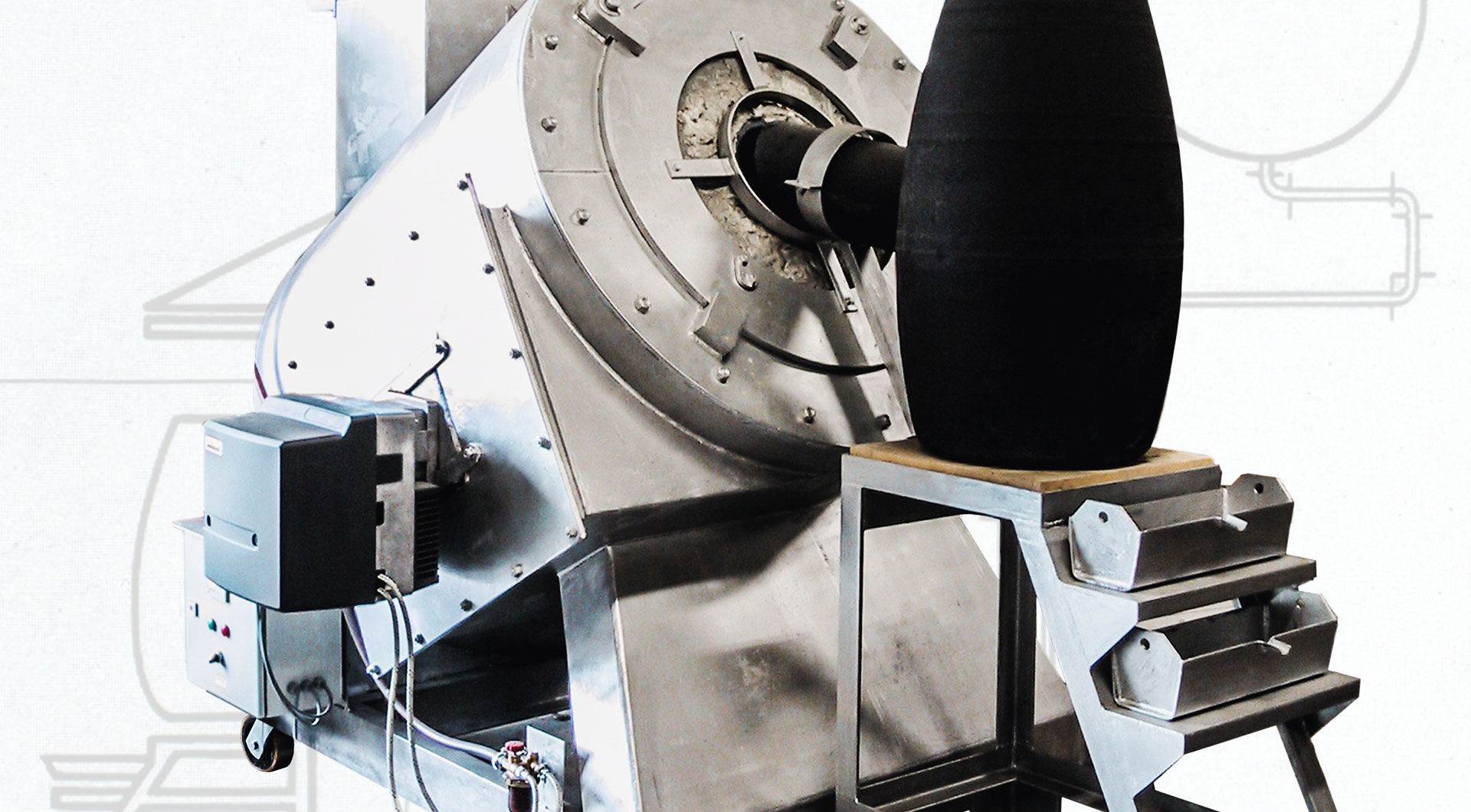

Application
Every galvanizing plant produces dross. Molten zinc dissolves iron, for example, from workpieces that are hot-dip galvanized, from the wall of the galvanizing kettle or from flux. It must be regularly removed out of the zinc bath.
Process
The zinc dross distillation furnace recovers 85-88% of the zinc bound in the dross with a purity of 99.9%. The furnace brings the zinc dross to evaporation temperature. The zinc is then condensed in the retort outside the furnace.
Benefits
- Improved quality, the galvanized surface is free of zinc dross spots
- Permanently optimum immersion depth in the galvanizing kettle
- Long kettle service life without overheating the kettle wall
- Excellent economy, especially with high zinc prices
- Environmental protection through recycling
Technical Specifications
Dimensions
- Length: 3,535 mm
- Width: 1,675 mm
- Depth: 2,040 mm
Process parameters
- Operating weight: ca. 450 kg/charge
- Daily capacity: ca. 1,000 kg
- Temperature: > 918 °C
Heating
- Natural gas or oil
Consumption
- Natural gas: 80 Nm³/charge
- Electricity: 30 kWh/charge

Product sheet Zinc Dross Distilling Furnace
Download (PDF)