Alu-Treat©
Aluminium bath treatment for high-pressure die or continuous casting
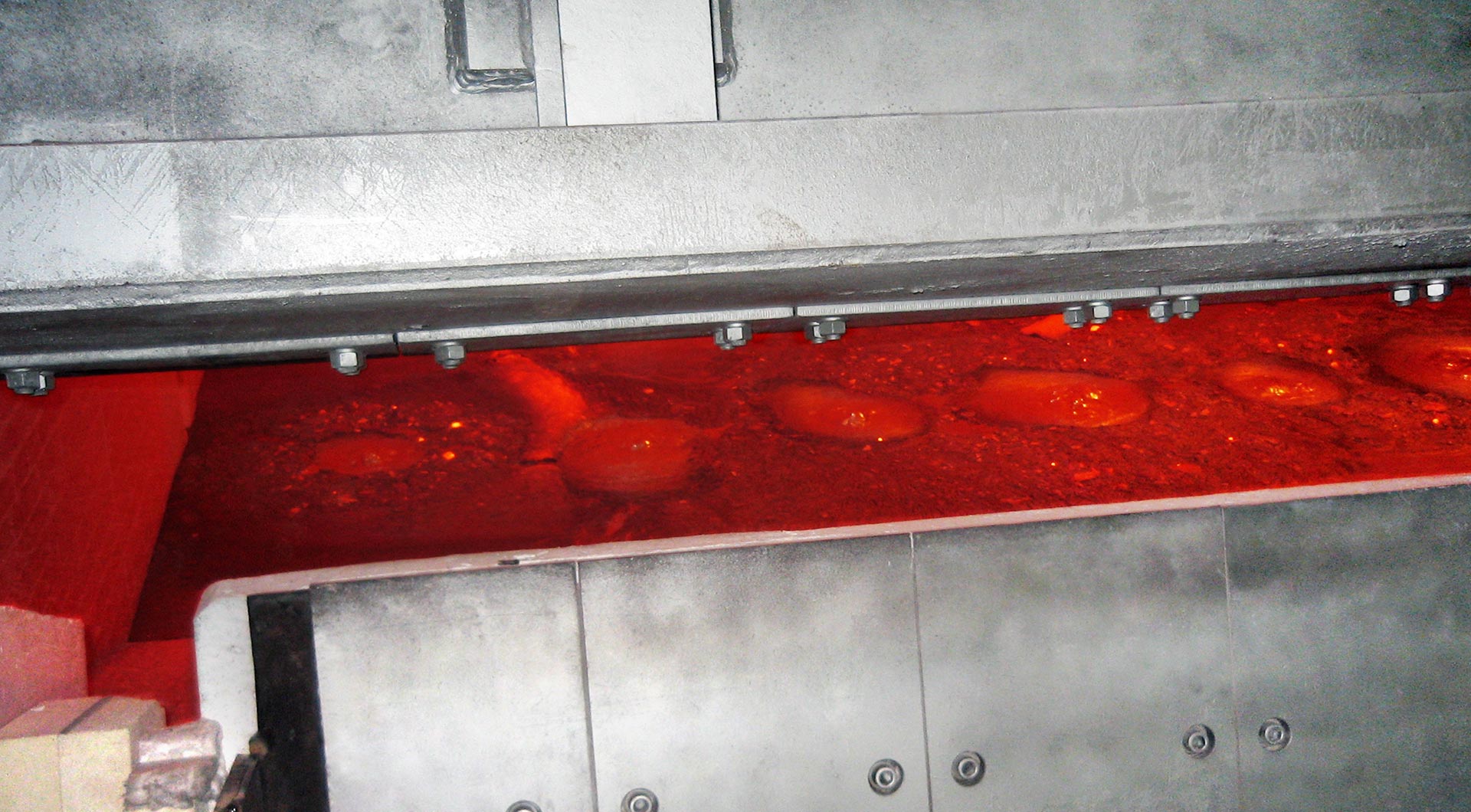
Clean solution:
Aluminium bath treatment for high-pressure die or continuous casting is utilised in casting furnaces of every make and ensures the production of superior-quality aluminium.
Design:
A porous refractory and aluminium-resistant stone is integrated in a gas-impermeable surround in the base of the furnace. Although porous, the stone prevents the penetration of any aluminium. A gas pipe leads into its underside. This is used to convey the cleaning gas which emerges from a gas control station into the porous stone, forming beads on the hot side in the form of fine bubbles.
Advantages:
- Improved cleanliness and homogeneity of the bath contents
- Typical density index value: approx. 1.5
- Reduction of other inclusions (STIC) by approx. 80%
- Minimised temperature differences above the bath height
- Higher furnace capacity
Superior-quality aluminium
Temporary operation of the furnace is also possible without cleaning gas. The advantage is that the stones have a particularly long service life – and recommissioning is problem-free. Argon is mainly used as a fuel gas. However, nitrogen can also be used as a cleaning gas if nitride formation (e.g. with magnesium) is not anticipated. The result is excellent: The aluminium is of a particularly high quality.
Three operating modes
The results in the furnace depend directly of the gas volume. Fundamentally speaking, there are three operating modes in this respect:
- Degassing, i.e. a low gas volume to reduce hydrogen in the bath
- Mixing/rinsing, i.e. a large gas volume for intensive mixing / cleaning of the bath
- Cleaning, i.e. a high gas pressure for periodic cleaning of the stone
Any casting furnace can be retrofitted with Alu-Treat©.

Product sheet Alu-Treat©
Download (PDF)