PulsReg®
Regenerator burner PR
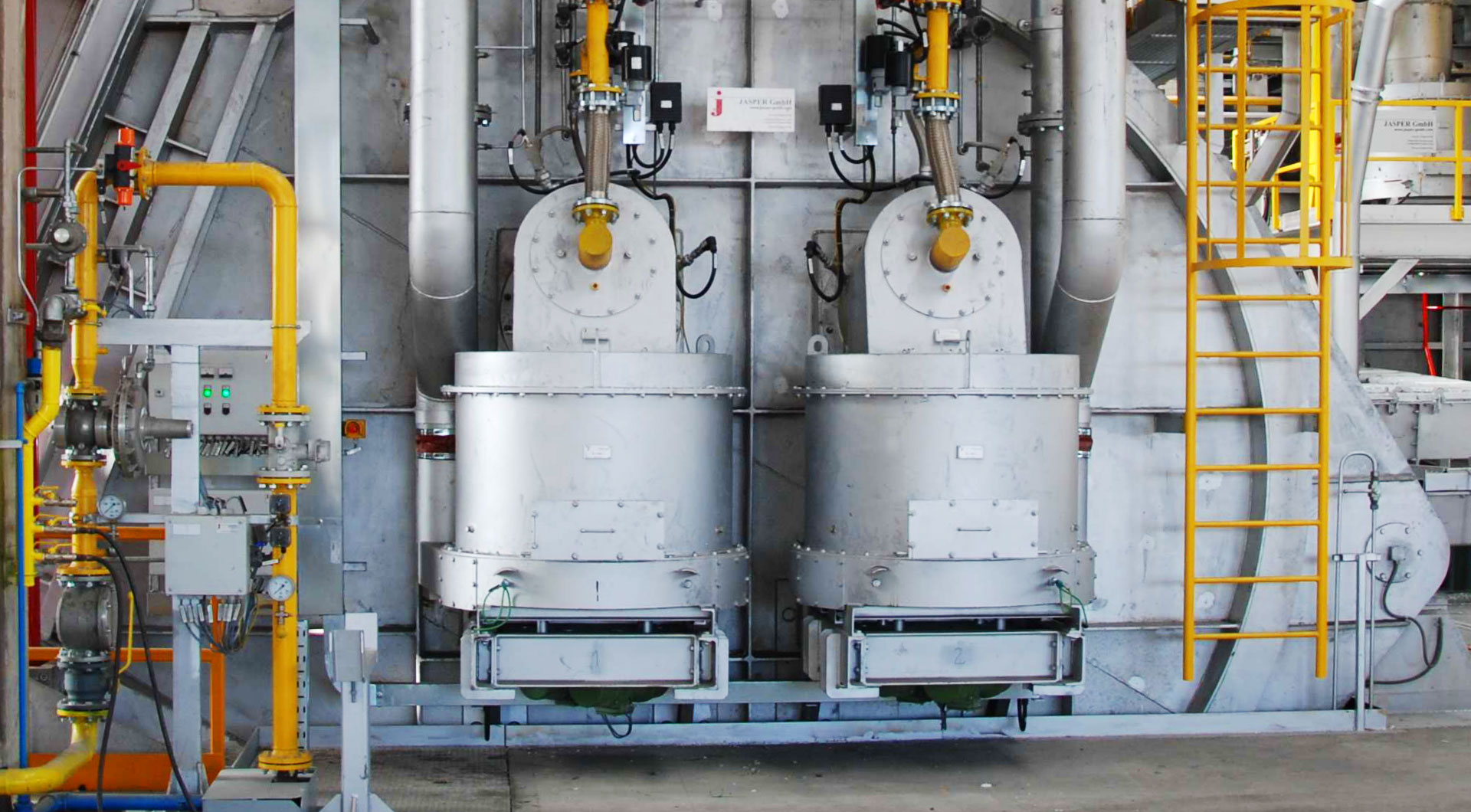
Specialist for aggressive and dusty furnace atmospheres – the classic in perfected engineering
PulsReg® has proven its value as a classic pulsed regenerator. The pulsed regenerative burner system is suitable for gas, oil and coal dust and designed especially for aggressive and dusty furnace atmospheres.
Advantages
- Extremely high level of efficiency
- Greater productivity
- Lower consumption
- Perfected technology
- CO2 reduction of up to 60%
- Air preheating up to 1,250 °C
Operational versatility
The product can be integrated in simple bath-type melting furnaces, hearth-type melting furnaces, casting furnaces and converters. A prerequisite is adequate space on the furnace that permits attachment of the two regenerators.
Availability > 98%
A separate waste gas fitting is required for the thermal equilibrium of the regenerators. One the one hand, this conveys up to 20% of the hot furnace gas away and, on the other, it also enables the emergency operation of a regenerator burner with cold air. This facilitates safe servicing and cleaning of the second burner. Furnace availability is increased as a result by over 98%.
Simple and safe handling
The burner and flame shape reflect precisely the furnace geometry. This enables the achievement of controllable burner capacities of up to 3,600 kW per pair.
Energy and cost savings
The PulsReg® generally achieves energy savings of 25–45% (at furnace temperatures of 900–1,050 °C). Installation of a regenerator burner also has a beneficial effect on smelting technology – particularly in the secondary aluminium industry. In combination with salt smelting furnaces, furnaces (collectors, converters, casting furnaces) equipped in this manner become cost-effective smelting systems for lumpy, compact scrap. Salt and dump costs can be saved to a considerable degree if skilful production planning has made adequate volumes of scrap available.
Enormously efficient: The fuel/air ratio control
Flow-managed fuel/air ratio control is absolutely necessary to minimise metal losses (burn off). The following estimation demonstrates why this is the case: given a production volume of 50,000 t/p.a. and increased burn of only 1%, the financial loss is already EUR 770,000! This is based on an aluminium price of EUR 1.54/kg. It is practically impossible to save as much anywhere else as through good fuel/air ratio control and regular maintenance.
PulsReg® / Function

PulsReg® consists of a burner pair, with a regenerator (heat exchanger) assigned to each burner. A regenerator of this nature consists of a container with refractory lining which contains heat accumulation padding.
Pulsating change of flow direction
One of the two regenerators heats up using furnace waste gas, while the other is cooled by the cold combustion air in the countercurrent. The combustion air heats up during this, is mixed with fuel in the burner, ignites and then heats the furnace.
When one of the two regenerators has been adequately heated, the flow direction in it changes and the regenerator heated with waste gas is cooled by air. Conversely, the regenerator which air has previously flowed through is heated up again with waste gas. The pulsating flow direction change in the regenerators occurs through valves (four-way control). Each burner is equipped in this respect with its own ignition and flame monitor pursuant to DIN/DVGW regulations.
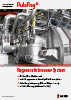
Product sheet PulsReg®
Download (PDF)